Are you experiencing issues with your truck that seem to pop up at the worst possible times? You’re not alone. From brake system failures to electrical malfunctions, truck problems can quickly turn from minor inconveniences to major headaches that keep your vehicle off the road.
The key to avoiding costly breakdowns lies in understanding the most common truck issues and implementing a regular maintenance schedule. Tires, brake systems, oil leaks, electrical systems, engine problems, clutch, suspension systems, exhaust systems, and batteries are the primary areas requiring consistent attention. By recognizing early warning signs—like squeaking brakes, transmission fluid leaks, or difficulty shifting gears—you’ll be better equipped to address problems before they escalate.
Common Truck Problems Every Owner Should Know
Transmission Issues
Transmission problems can quickly escalate from minor inconveniences to major repairs. Watch for warning signs like your truck repeatedly popping out of gear, leaking transmission fluid, difficulty shifting, grinding noises, or weakening acceleration. Getting your truck to a repair shop at the first sign of transmission trouble prevents costly breakdowns and extensive damage.
Tire Blowouts
Tire blowouts are inevitable for trucks logging thousands of miles. Over or under-pressurized tires rank among the most frequent truck problems mechanics encounter. Check tire pressure regularly, inspect for wear patterns, and rotate tires according to your manufacturer’s schedule to extend their life and reduce blowout risks.
Brake System Failures
Brake issues are especially concerning given the stopping demands of heavy-load trucks. Common indicators include squeaking noises, soft pedals, or vibrations while braking. These symptoms typically point to worn-out brake pads or problems with brake fluid. Inspect your brakes regularly, replace pads as needed, and check fluid levels to maintain optimal stopping power.
Electrical System Malfunctions
Today’s trucks rely on complex electronic systems that can malfunction unexpectedly. Dead batteries, faulty alternators, and blown fuses frustrate many truck owners. Prevent electrical problems by checking your battery connections regularly, ensuring wire connections remain secure, and carrying spare fuses for emergencies. When electrical issues persist, consulting a professional mechanic often saves time and prevents further complications.
Engine Problems
Engine issues manifest through unusual noises, decreased power, excessive smoke, or poor fuel efficiency. Regular oil changes and filter replacements are critical for preventing engine damage. Listen for knocking sounds, watch your temperature gauge, and address check engine lights promptly to avoid catastrophic engine failures.
Clutch Complications
Clutch problems appear as difficulty changing gears, slipping, or strange noises when pressing the clutch pedal. These components naturally wear down with use, especially in trucks under heavy loads or in stop-and-go traffic conditions. Adjusting your driving habits can extend clutch life, but eventual replacement is part of normal truck maintenance.
Suspension System Issues
Failing suspension components result in uncomfortable rides, uneven tire wear, and handling difficulties. Listen for clunking noises when driving over bumps and check for uneven vehicle stance. Regular inspection of shocks, struts, and leaf springs helps identify suspension problems before they affect your truck’s stability and safety.
Exhaust System Defects
Exhaust leaks create dangerous conditions through potential carbon monoxide infiltration and reduced fuel efficiency. Unusual exhaust noises, visible damage, or increased engine volume often indicate exhaust system problems. Inspect your exhaust components regularly, focusing on connections and muffler condition to prevent harmful emissions and performance issues.
Battery Failures
Battery problems typically emerge during cold weather or after periods of disuse. Corrosion around terminals, slow cranking, or dashboard warning lights suggest battery issues. Clean terminals regularly, check electrolyte levels in conventional batteries, and have your charging system tested annually to avoid unexpected battery failures when you’re far from assistance.
Tire Issues and Blowouts
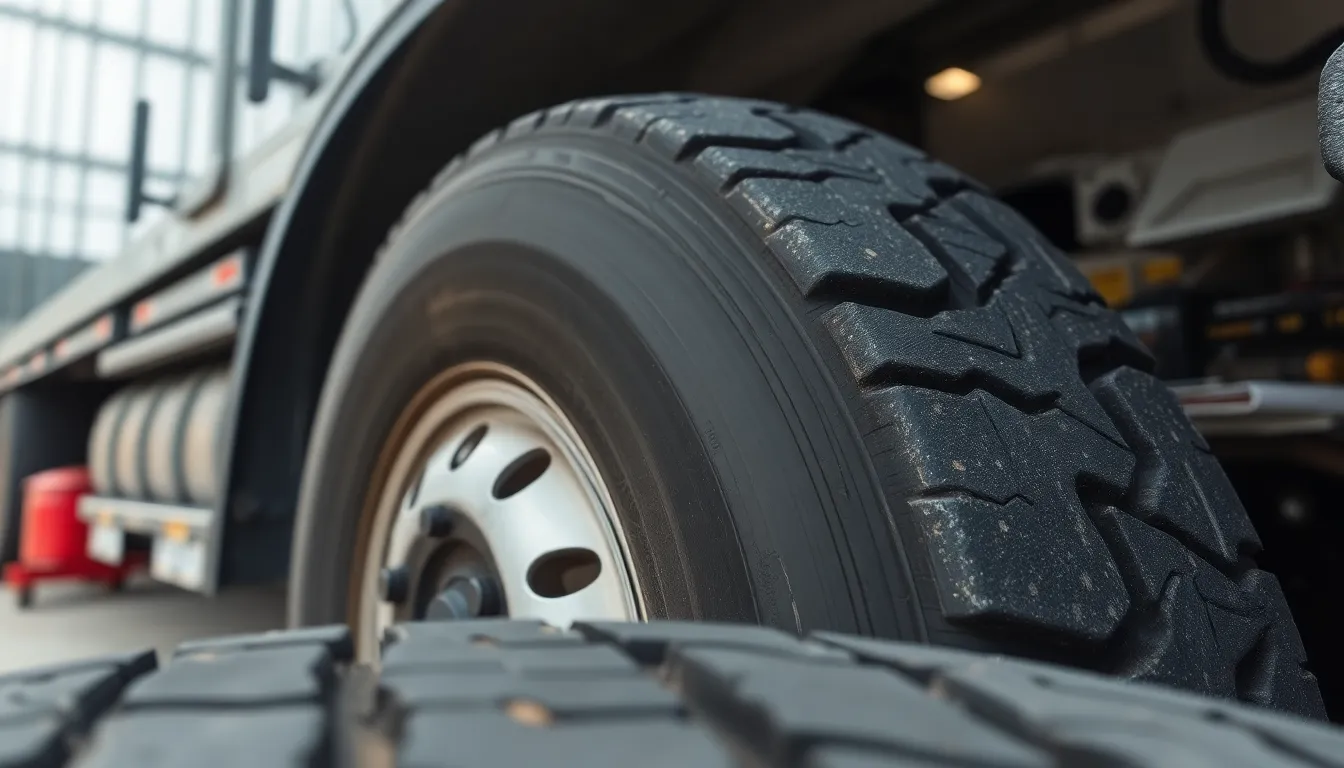
Tire problems rank among the most common and dangerous truck issues on the road today. According to recent data, 51.3% of all emergency road calls from truckers are for flat or blown-out tires, making them the leading cause of unexpected downtime for commercial vehicles.
Signs of Tire Problems
Identifying tire issues early helps prevent dangerous blowouts and costly roadside emergencies. Watch for these warning signs:
- Uneven wear patterns across the tire surface, indicating potential alignment or suspension problems
- Visible cracks or bulges in the sidewalls that suggest structural weakening
- Shallow tread depth below the recommended minimum, reducing traction and increasing blowout risk
- Vibration or shaking while driving, often pointing to tire imbalance or internal damage
- Repeated pressure loss requiring frequent inflation, signaling slow leaks or valve issues
- Visible foreign objects like nails or screws embedded in the tread
Tire problems often manifest subtly before catastrophic failure occurs. Regular visual inspections during pre-trip checks catch many of these issues before they escalate into major truck problems.
Prevention and Maintenance
Proactive tire maintenance significantly reduces blowout risks and extends tire life. Implement these essential practices:
- Maintain proper tire pressure by checking before and after major trips. Both overinflation and underinflation increase blowout risk and reduce tire lifespan.
- Schedule regular professional inspections with diesel mechanics who can identify misaligned axles, shallow tread depth, and other problems that contribute to tire failures.
- Rotate tires according to manufacturer recommendations to ensure even wear patterns.
- Replace worn tires promptly when they show signs of aging or when tread depth becomes dangerously low.
- Align axles properly during maintenance visits to prevent uneven wear that weakens tire structure.
- Monitor load distribution to avoid overloading specific tires, which increases failure risk.
The enormous weight of commercial trucks makes proper tire maintenance vital for road safety. A blown tire can cause a truck to fishtail, potentially triggering jackknife accidents or dangerous rollovers. Because of their size, commercial vehicles with tire failures can create multi-car pileups if the driver loses control. By implementing consistent tire maintenance protocols, fleet managers and owner-operators significantly reduce these risks while extending tire life and improving fuel efficiency.
Brake System Failures
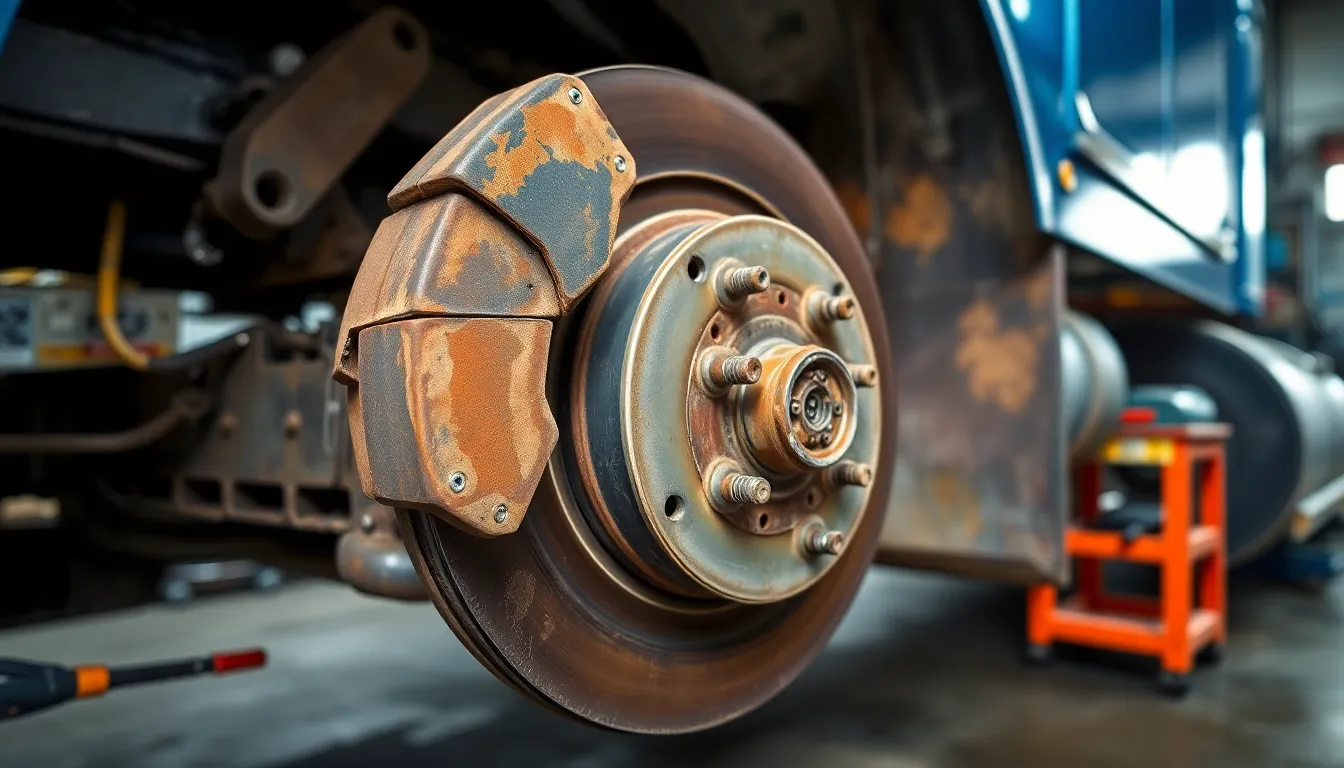
Brake system failures rank as one of the leading factors in large truck crashes according to data from the Federal Motor Carrier Safety Association. Air brake failures specifically account for 30% of all commercial vehicle crashes, making brake maintenance a critical safety concern for all truck operators.
Symptoms of Brake Problems
Brake problems manifest through several distinct warning signs that shouldn’t be ignored. Squeaking noises during braking indicate worn-out brake pads that require immediate replacement. A soft or spongy brake pedal suggests air in the brake lines or low fluid levels. Vibrations felt through the brake pedal point to warped rotors or uneven pad wear. If your truck pulls to one side during braking, you’re likely experiencing uneven brake wear or a stuck caliper. Increased stopping distance and reduced braking effectiveness signal deteriorating brake components that compromise safety, especially when carrying heavy loads.
Critical Brake Components
Several key components in a truck’s braking system require regular inspection and maintenance. Brake pads and shoes wear down over time and need replacement before they’re completely depleted. Brake fluid levels must remain adequate, with no leaks present in the system. The brake calipers, which apply pressure to the brake pads, can seize or become damaged through regular use. Rotors and drums develop grooves, cracks, or warping from heat and friction. Air brake systems specifically contain components like drain valves, wet tanks, glad hands, slack adjusters, pushrods, and ABS connectors that require systematic inspection.
Regular maintenance prevents catastrophic brake failures by identifying worn components before they fail completely. For air brake systems, inspect the drain valve and wet tank to ensure no valve failure occurs in primary or secondary circuits. Remove any buildup of dirt, debris, or salt near the glad hands. Examine rubber boots and seals around ABS connectors for signs of wear. Check slack adjusters and pushrods for proper functionality, observing pushrod actuation from brake chambers and looking for broken springs. Inspect all parking brakes for chamber leaks.
Driver error contributes significantly to brake failures, particularly when operators ride the brakes down steep hills for extended periods, causing overheating or even fires. Inexperienced drivers unfamiliar with jake brake operation face higher risks of brake-related incidents. The tremendous weight commercial trucks carry places intense pressure on braking systems, accelerating wear and making regular comprehensive maintenance essential for safe operation.
Engine Troubles
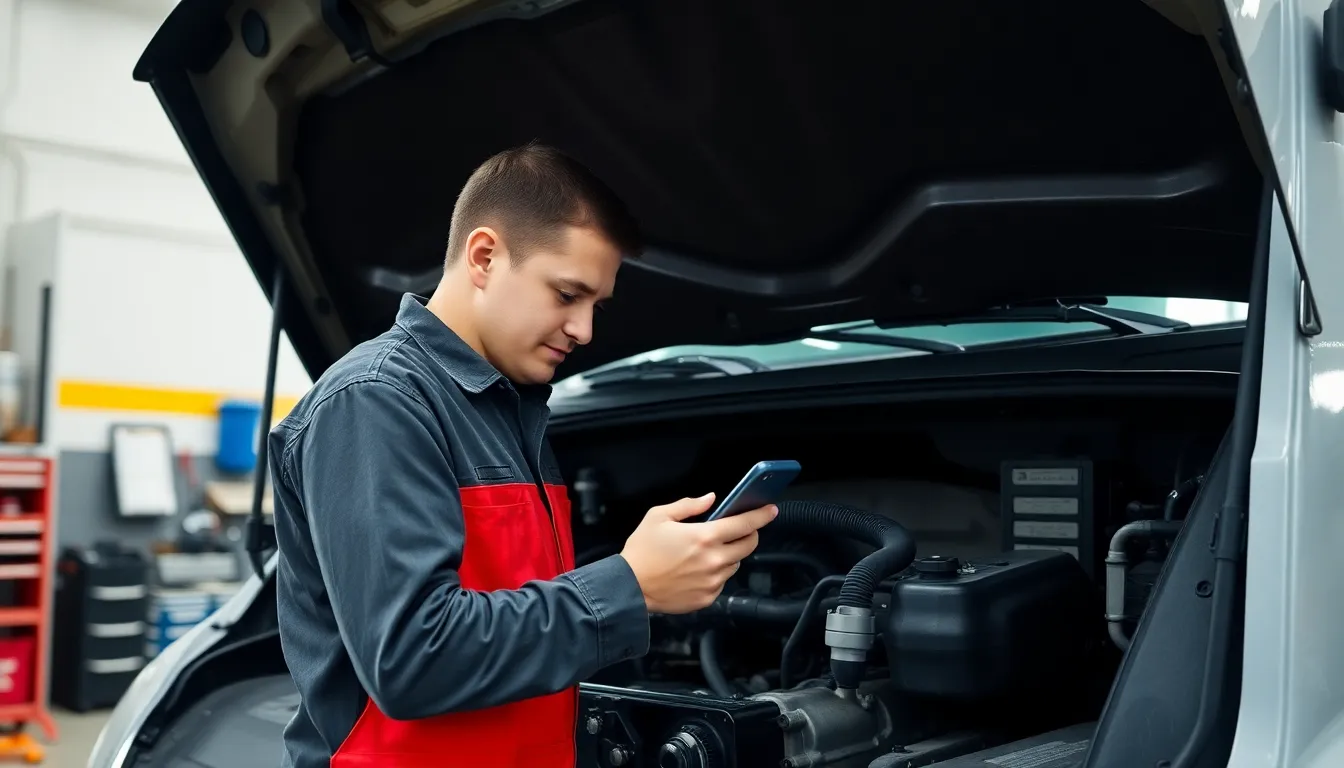
Engine troubles rank among the most severe truck problems that fleet owners encounter. Truck engines are designed to operate for over one million miles with proper maintenance, compared to car engines which typically last only 200,000 miles. Understanding common engine issues and their warning signs can help prevent costly breakdowns and extend your truck’s lifespan.
Overheating Causes
Overheating in truck engines stems from several common issues that require immediate attention. Leaking coolant, faulty thermometers, and old radiators frequently cause engine temperature spikes. Defective cooling fans, often resulting from easily fixable electrical problems, also contribute to overheating. Other culprits include water pump failures, blown gaskets, and engine component damage. A professional inspection helps reveal the exact cause of overheating, which if left unchecked, leads to engine failure and potential accidents. Regular monitoring of your temperature gauge and watching for steam from the hood identifies problems early before they escalate into major repairs.
Oil Leaks and Their Impact
Oil leaks create serious damage to truck engines even when not immediately visible. When oil escapes, your truck loses crucial lubrication that protects moving components. This increased friction between engine parts accelerates wear and can ultimately cause complete engine failure. Oil leaks often indicate larger issues such as broken gaskets or cracked seals that require professional repair. Additionally, diesel trucks that sit idle for extended periods face oil oxidation, where air creates bubbles and contaminants in the oil, reducing its lubricating effectiveness. Regular oil changes and maintenance checks help identify leaks before they cause significant damage, ensuring your truck’s engine performs reliably throughout its service life.
Electrical System Problems
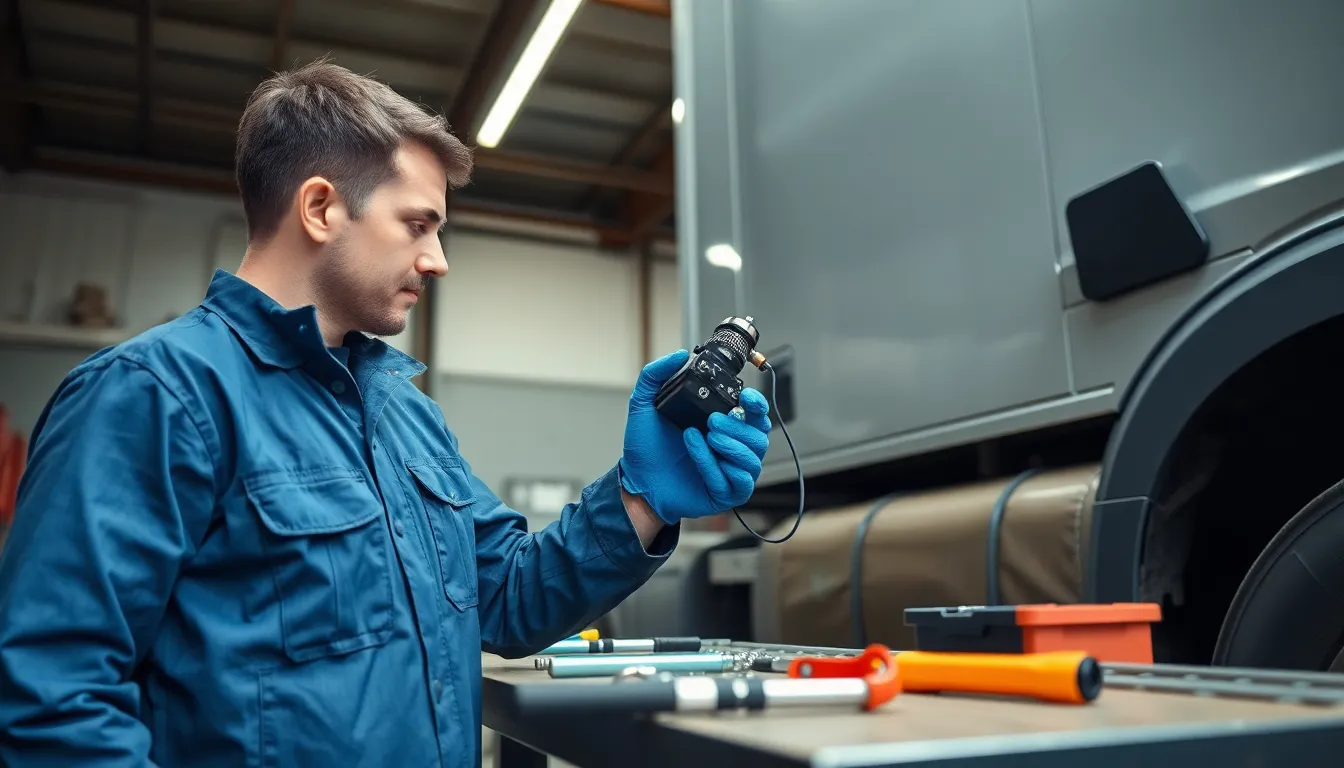
Electrical system failures rank among the most common truck problems, often leaving vehicles inoperable at inconvenient times. The electrical system consists of three vital components: the starter motor, alternator, and battery—if any one fails, your truck stops functioning.
Battery and Alternator Issues
Battery and alternator problems frequently plague truck owners and fleet managers. A failing battery shows several warning signs: corrosion around the connections, difficulty starting the engine, dim or flickering lights, and unusual clicking noises during ignition attempts. The alternator, responsible for charging your battery while the engine runs, typically fails gradually with symptoms like dashboard warning lights, dimming headlights, or strange whining noises from the engine compartment.
To prevent these electrical truck problems:
- Measure battery power regularly with a multimeter
- Perform load tests to evaluate battery capacity
- Check for voltage drops that indicate charging issues
- Replace weak or dead batteries immediately
- Inspect the alternator belt for proper tension and wear
- Clean battery terminals to prevent corrosion buildup
Wiring and Connection Failures
Wiring issues cause frustrating intermittent truck problems that can be difficult to diagnose. Modern commercial trucks contain extensive wiring networks vulnerable to damage from vibration, temperature fluctuations, and exposure to elements. Common wiring problems include short circuits, loose connections, and corroded terminals.
Warning signs of wiring and connection failures include:
- Intermittent electrical component operation
- Strange smells (especially burning odors)
- Blown fuses that repeatedly fail after replacement
- Unexplained battery drain
- Dashboard warning lights that appear randomly
- Electrical components that work inconsistently
For complex electrical systems in commercial trucks, professional diagnosis often provides the most efficient solution. While you can perform basic checks like securing wire connections and inspecting for visible damage, a qualified technician should handle comprehensive electrical system repairs to prevent cascading failures that could leave your truck stranded.
Transmission and Clutch Complications
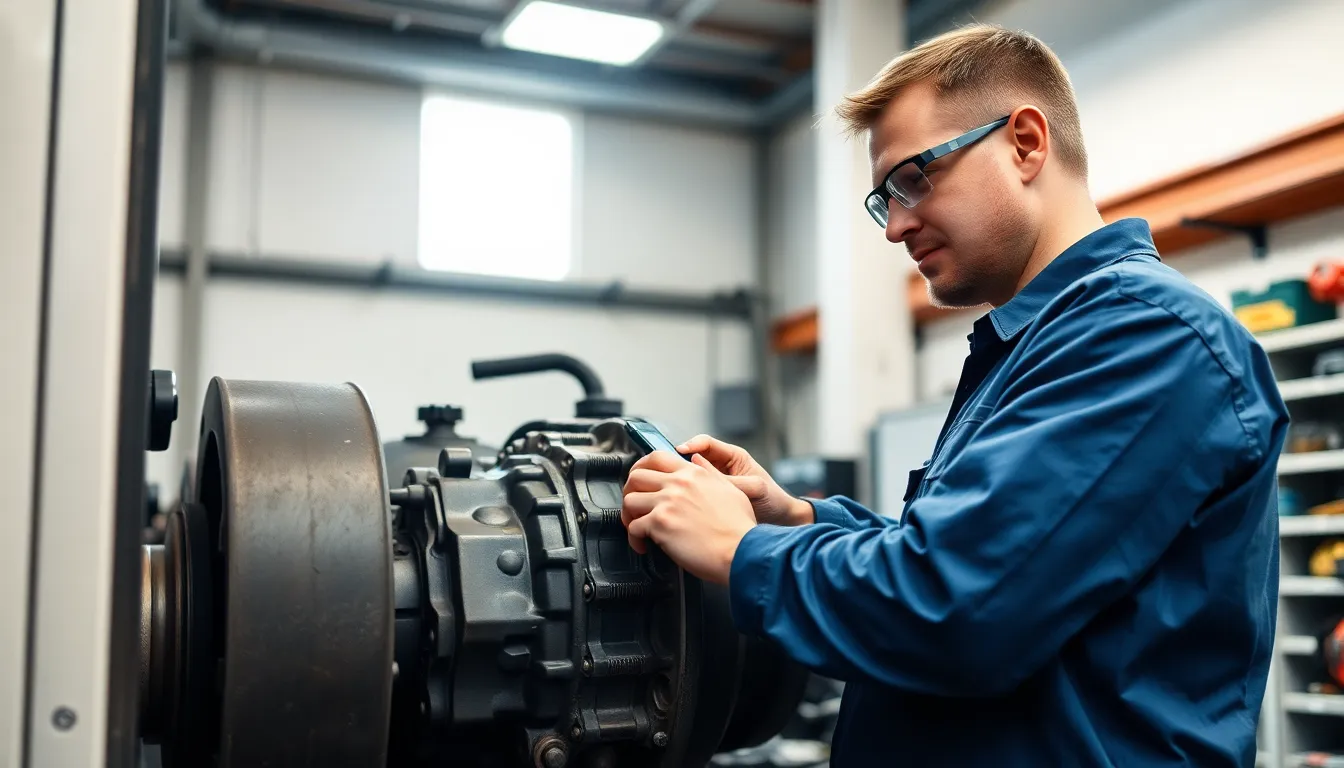
Transmission and clutch issues rank among the most serious truck problems that can quickly escalate from minor concerns to major breakdowns. These components bear enormous stress during daily operations, especially in commercial trucks used for heavy hauling and long-distance transport.
Warning Signs of Transmission Failure
Transmission failures rarely occur without warning signs. Recognizing these early indicators can save thousands in repair costs and prevent roadside emergencies. Common warning signs include:
- Repeatedly popping out of gear during operation, which indicates internal component wear
- Leaking transmission fluid under your truck, often appearing as red or brown puddles
- Difficulty shifting into gear or unusual resistance when changing gears
- Grinding sounds coming from the transmission during gear changes
- Weakening acceleration or slipping gears under load
- Delayed shifting between gears when accelerating
- Burning smell during operation, indicating overheating transmission fluid
Regular transmission fluid checks and changes are essential for maintaining optimal transmission performance. The fluid should be at the correct level and free of particles, with a bright red color rather than dark or burnt-looking. When you notice any unusual behavior, consulting a mechanic for a thorough inspection prevents more severe damage that could sideline your truck.
Clutch Wear and Tear
Clutch components deteriorate naturally over time, especially in commercial trucks that experience heavy use. Fleet drivers spending extensive hours on the road inevitably face clutch complications due to accumulated wear and tear. Several factors contribute to premature clutch failure:
- Extended service time – The clutch is designed to wear gradually, with time being a primary factor in breakdowns
- Improper driving habits – Riding the clutch or aggressive shifting accelerates wear
- Heavy loads – Consistently hauling maximum capacity puts additional strain on clutch components
- Stop-and-go traffic – Frequent engagement and disengagement in urban driving conditions increases wear
- Poor maintenance – Neglecting regular adjustments and inspections leads to undetected issues
You can extend clutch life by following manufacturer recommendations for usage and practicing safe driving habits. Using the clutch according to specifications reduces premature wear. Pre-trip inspections that include checking for proper clutch pedal free play and unusual resistance during shifting help identify potential problems before they become critical. Addressing transmission and clutch issues promptly not only prevents costly repairs but also ensures your truck remains reliable for daily operations.
Suspension Problems
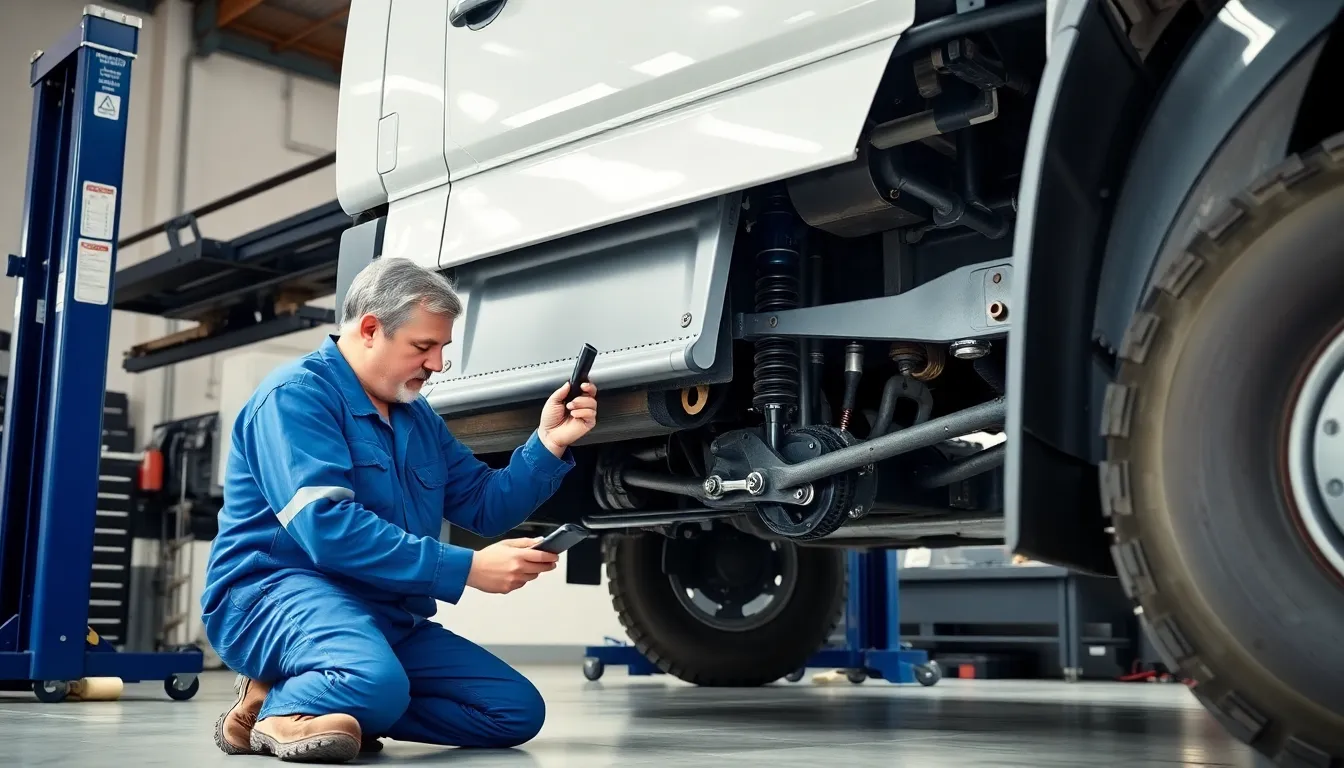
Truck suspension systems absorb road irregularities, ensuring a smooth, balanced ride. When suspension components wear out or fail, they create numerous performance issues that affect both comfort and safety. These suspension problems rank among the most common truck issues requiring consistent maintenance and timely repair.
Handling and Stability Issues
Suspension and steering systems work together to maintain truck stability. When suspension components fail, your truck may wander instead of tracking straight or feel loose when steering. This instability creates dangerous driving conditions, especially at highway speeds or when carrying heavy loads. You’ll notice the vehicle bouncing excessively over bumps or nosediving during braking. A simple test involves pushing down on the front and back bumpers when parked – the truck should return to its original height with minimal bounce. Excessive bouncing indicates worn shocks, springs, or struts that compromise handling and require professional inspection.
Suspension Component Failures
Suspension components naturally wear out over time and require regular replacement to maintain truck performance. Tie rod ends, suspension bushings, shocks, and struts commonly fail after extended use. When bushings deteriorate, they allow suspension parts to rattle and create persistent banging, squeaking, or clunking noises from beneath your truck. These sounds indicate suspension components need servicing. Driving with failing suspension bushings and tie-rod ends for extended periods strains other parts of the system, creating a cascade of truck problems. Unlike engines and transmissions built to last the vehicle’s lifetime with minimal maintenance, suspension components need regular attention to prevent more serious handling issues. Professional diagnostic testing is often necessary to determine exactly which components require replacement when suspension problems appear.
Exhaust System Concerns
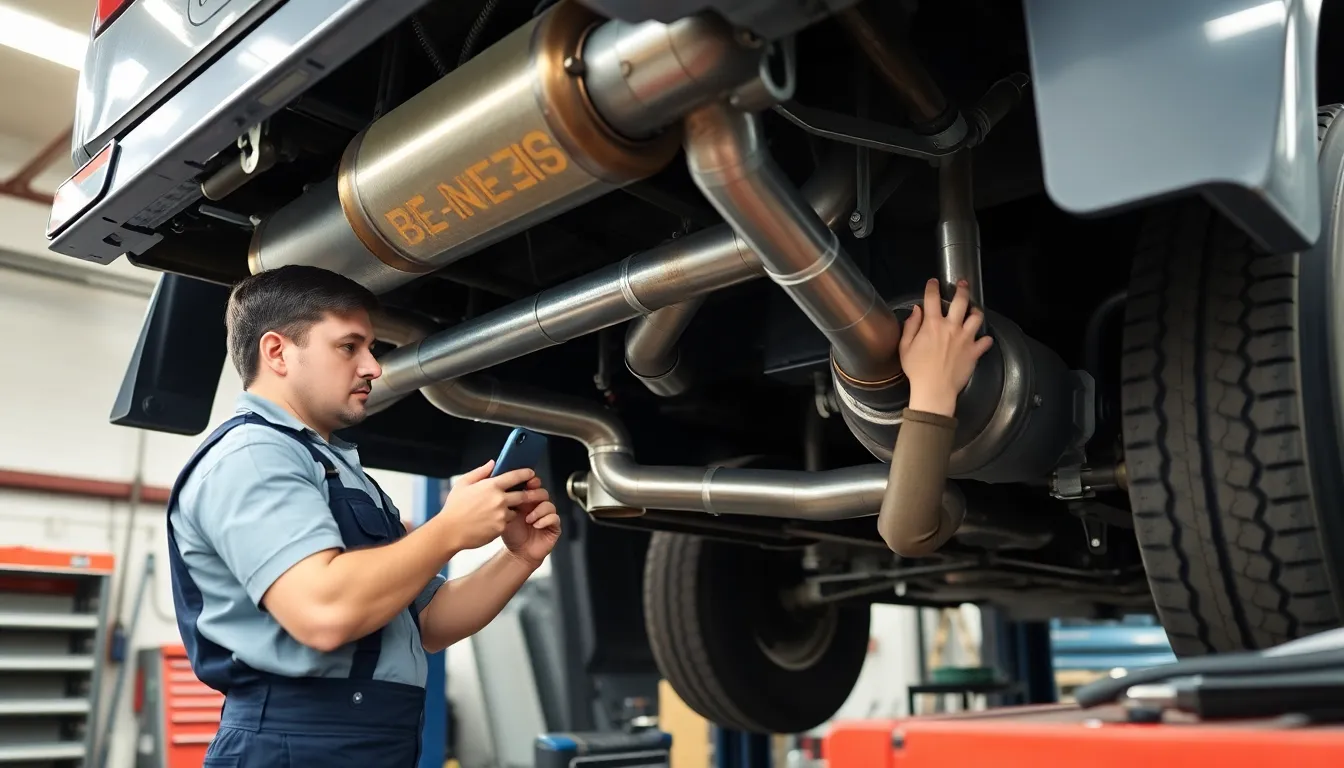
Exhaust system problems in trucks can lead to decreased performance, environmental violations, and safety hazards. These issues often go undetected until they cause significant damage or trigger warning lights on your dashboard.
Performance Impact
Exhaust system malfunctions directly affect your truck’s performance and fuel efficiency. Clogged exhaust pipes restrict airflow, creating back pressure that forces your engine to work harder and consume more fuel. Common signs of exhaust problems include unusual engine noises, decreased acceleration, and reduced power when climbing hills. A damaged exhaust manifold or cracked pipes can cause loud rumbling sounds that intensify during acceleration. If left unaddressed, these truck problems can lead to overheating and eventual engine damage, requiring costly repairs.
Pre-trip inspections help identify early warning signs of exhaust issues, such as black soot around pipe connections or visible rust and corrosion. Regular maintenance checks on your exhaust system components—including the manifold, pipes, muffler, and catalytic converter—prevent minor issues from escalating into major truck problems that could leave you stranded.
Environmental Considerations
Your truck’s exhaust system plays a critical role in controlling emissions and meeting environmental regulations. Faulty exhaust components lead to increased pollution and can result in failed emissions tests or DOT violations. The catalytic converter, a key component of modern exhaust systems, reduces harmful gases by converting them into less toxic substances before they exit your truck.
White or blue smoke from your exhaust indicates burning coolant or oil, while excessive black smoke points to improper fuel combustion. These emissions not only harm the environment but also signal underlying truck problems that require immediate attention. Replacing cabin air filters and maintaining other exhaust components ensures compliance with Federal Motor Carrier Safety Association (FMCSA) regulations for healthy emissions.
Particle filters in diesel trucks need regular cleaning or replacement to function effectively. Statistics show that well-maintained exhaust systems reduce particulate emissions by up to 90% compared to failing systems. By addressing exhaust system concerns promptly, you’re protecting both your truck’s performance and contributing to cleaner air quality while avoiding potential fines for non-compliance with emissions standards.
Preventative Maintenance Tips
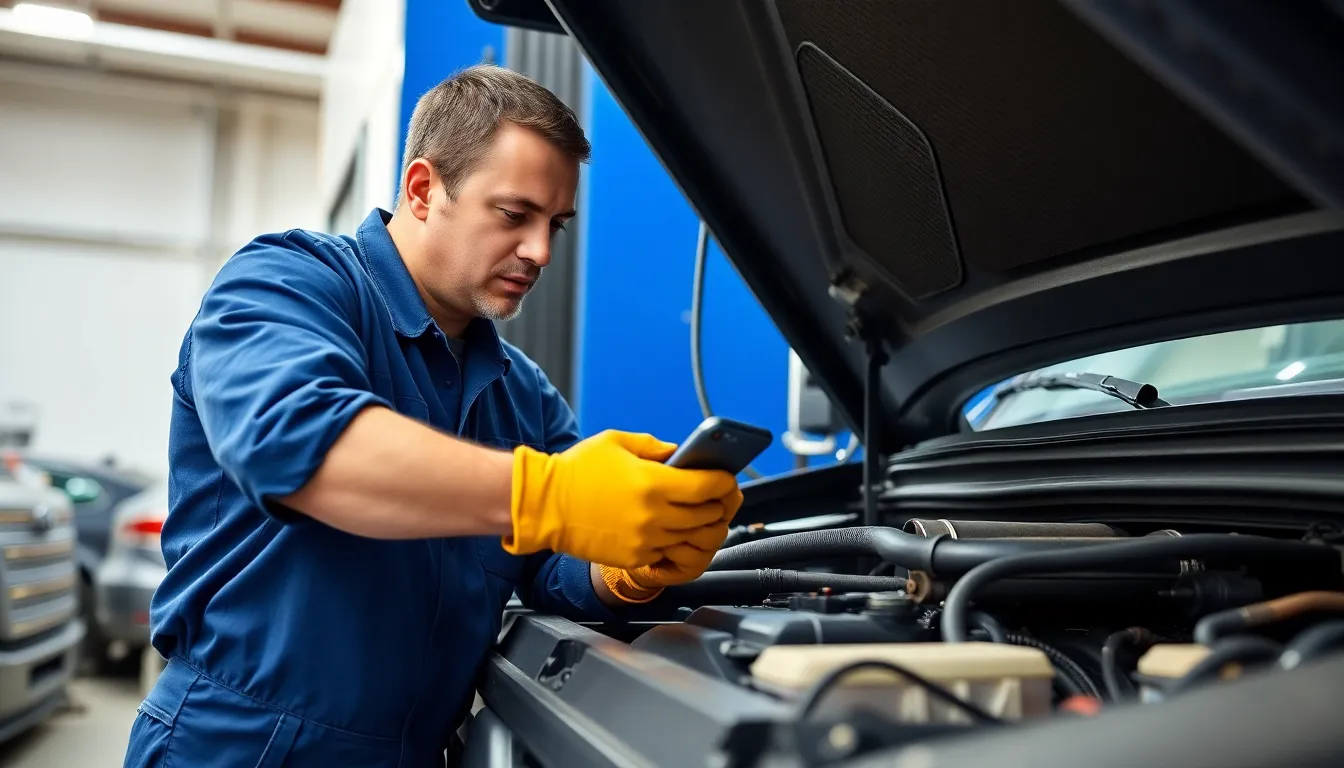
Preventative maintenance is the cornerstone of avoiding costly truck problems and extending your vehicle’s lifespan. Regular upkeep not only prevents unexpected breakdowns but also maintains optimal performance and safety on the road.
Regular Inspection Schedule
Creating a consistent inspection schedule for your truck dramatically reduces the likelihood of developing serious problems. Check your tires, brakes, fluids, and electrical systems weekly for early signs of wear or damage. Monthly inspections should include more thorough examinations of your suspension, exhaust system, and engine components. Quarterly checks need to focus on transmission, clutch, and cooling systems to ensure everything operates properly.
Maintenance intervals also depend on mileage milestones:
- Every 3,000-5,000 miles: Oil and filter changes
- Every 6,000 miles: Tire rotation
- Every 15,000 miles: Air filter replacement
- Every 30,000 miles: Transmission fluid check
- Every 60,000 miles: Brake fluid replacement
Document all inspections and maintenance work in a logbook to track your truck’s service history and identify recurring issues. Many fleet managers use digital maintenance tracking tools to receive automatic alerts when service is due, eliminating guesswork about when specific components need attention.
DIY vs. Professional Repairs
While performing some maintenance tasks yourself saves money, certain truck problems require professional expertise. Basic DIY maintenance includes checking tire pressure, inspecting belts and hoses, replacing wiper blades, and monitoring fluid levels. These simple checks prevent minor issues from escalating into major truck problems.
Professional technicians handle more complex issues involving:
- Electrical system diagnostics
- Engine repair and overhauls
- Transmission servicing
- Brake system repairs
- Suspension and alignment work
Consider these factors when deciding between DIY and professional repairs:
- Complexity of the issue
- Tools required for proper diagnosis
- Time constraints and urgency
- Warranty considerations
- Safety implications
Even if you’re mechanically inclined, establishing a relationship with a trusted diesel mechanic provides a valuable resource when truck problems exceed your expertise. Professional technicians possess specialized diagnostic equipment and training to identify problems that might go unnoticed during regular DIY inspections.
Finding the right balance between DIY maintenance and professional service ensures your truck remains reliable while managing repair costs effectively. Remember that preventative maintenance costs significantly less than emergency repairs and reduces the likelihood of breakdown-related downtime.
Conclusion
Truck problems don’t have to derail your operations or compromise safety on the road. By staying vigilant about warning signs and implementing a consistent maintenance schedule you’ll catch minor issues before they escalate into major failures.
Remember that your truck’s reliability depends on how well you care for its critical systems—from tires and brakes to engine and electrical components. A proactive approach saves money prevents dangerous breakdowns and extends your vehicle’s lifespan.
Invest time in regular inspections build a relationship with a qualified mechanic and keep detailed maintenance records. Your commitment to preventative care isn’t just good business practice—it’s essential for keeping your truck running smoothly for those million-plus miles it was designed to deliver.
Frequently Asked Questions
What are the most common truck problems owners face?
The most common truck problems include brake system failures, tire issues, engine troubles, transmission problems, electrical malfunctions, suspension system issues, and exhaust system defects. Tire problems account for over half of emergency road calls, while air brake failures cause 30% of large truck crashes. Regular maintenance is crucial to prevent these issues from escalating into costly repairs.
How can I identify brake problems in my truck?
Look for warning signs such as squeaking noises, soft brake pedals, vibrations when braking, and increased stopping distances. These symptoms indicate potential issues with brake pads, calipers, or rotors. Since brake failures account for 30% of large truck crashes, addressing these signs immediately is critical for safe operation.
What are the early warning signs of tire problems?
Watch for uneven wear patterns, visible cracks or bulges, shallow tread depth (below 4/32 inch), vibrations while driving, and repeated pressure loss. These signs indicate potential tire issues that could lead to dangerous blowouts. Since tire problems account for over half of all emergency road calls, recognizing these warnings early can prevent roadside emergencies.
How can I prevent tire blowouts?
Maintain proper tire pressure according to manufacturer specifications, schedule regular professional inspections, rotate tires at recommended intervals, replace worn tires promptly, ensure proper axle alignment, and monitor load distribution. Proactive tire maintenance is essential for road safety and can significantly extend tire life while reducing blowout risks.
What causes truck engines to overheat?
Truck engines typically overheat due to leaking coolant, faulty thermometers, old radiators, or defective cooling fans. Regular coolant checks and professional inspections can identify these issues before they cause engine failure. With proper maintenance, truck engines can last over one million miles, making preventative care extremely valuable.
How serious are oil leaks in trucks?
Oil leaks are serious indicators of potential larger issues like broken gaskets or cracked seals. They reduce lubrication and increase friction between engine parts, which can lead to catastrophic engine damage. Regular oil changes and maintenance checks help identify leaks early and ensure reliable engine performance.
What are common electrical system problems in trucks?
The most common electrical issues involve the three vital components: starter motor, alternator, and battery. Warning signs include corrosion on battery terminals, difficulty starting the vehicle, and dimming lights. Regular battery power checks and alternator belt inspections can prevent electrical failures that could leave your truck inoperable.
How can I identify transmission problems?
Watch for difficulty shifting gears, leaking transmission fluid, grinding or whining sounds, delayed engagement, and burning smells. These symptoms indicate potential transmission failure, which can escalate quickly if not addressed. Regular fluid checks and consulting a mechanic when these signs appear can prevent costly transmission replacements.
What maintenance schedule should truck owners follow?
Create a consistent inspection schedule based on mileage milestones: basic checks every 3,000-5,000 miles, intermediate service at 15,000-30,000 miles, and major overhauls at 100,000+ miles. Document all inspections in a logbook and balance DIY maintenance with professional repairs. Regular preventative maintenance is significantly less expensive than emergency repairs.
When should I consult a professional mechanic versus DIY repairs?
Handle basic maintenance like fluid checks, tire pressure monitoring, and visual inspections yourself. For complex issues involving brakes, transmission, electrical systems, or engine performance, consult a professional diesel mechanic. Establishing a relationship with a trusted mechanic ensures reliable truck operation and helps manage repair costs effectively.